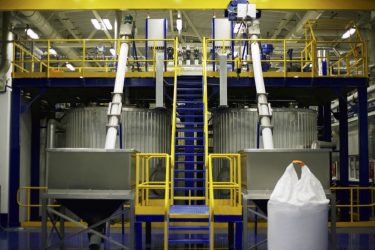
Trasporto granuli in plastica: tipologie e alternative
La plastica, grazie alla sua versatilità e ai costi contenuti, è diventata uno dei materiali più utilizzati nell’industria moderna.
La sua diffusione ha trasformato radicalmente numerosi settori portando la lavorazione e il suo trasporto a rappresentare fasi critiche nei processi produttivi, richiedendo un’attenzione particolare per garantire qualità e sostenibilità.
In Italia, molte aziende sono coinvolte in questa filiera, pertanto si trovano ad affrontare sfide e opportunità legate alla gestione efficiente e responsabile di questo materiale.
Per questo motivo, il trasporto dei granuli è diventato un passaggio fondamentale nell’industria della plastica, cruciale per assicurare la fluidità delle operazioni di produzione.
Le aziende sono consapevoli dell’importanza di questa fase per ottimizzare costi e tempi, oltre che a preservare la qualità del materiale.
In questo articolo esploreremo i vari sistemi per il trasporto dei granuli, concentrandoci poi sulle diverse soluzioni e le possibili implementazioni di strumenti che permetteranno di avere un macchinario completo ed efficace.
Tipologie e alternative di trasporto dei granuli di plastica
Quando si parla di trasporto nelle aziende che trattano la plastica, ci si riferisce agli strumenti e ai macchinari utilizzati per trasferire la materia da un punto all’altro.
Il trasporto dei granuli plastici può essere gestito attraverso diverse modalità, ognuna con i propri vantaggi e svantaggi.
Le principali scelte possono ricadere su:
- Trasporto manuale.
Questo metodo, il più tradizionale, consiste nel trasporto e svuotamento manuale dei sacchi. Non necessita di manodopera specializzata e comporta costi di lavoro ridotti, ma richiede più tempo ed espone a rischi di sprechi, contaminazione del materiale e problemi di sicurezza. - Trasporto in pressione.
Impiega pompe ad aria compressa per spingere i granuli di plastica attraverso tubazioni e contenitori. Consente una velocità di trasporto maggiore, con una portata di oltre 1000 kg/h. Solitamente prevede stazioni singole e richiede manutenzione periodica del filtro ciclonico o di altri sistemi filtranti. - Trasporto meccanico.
Utilizza sistemi meccanici come coclee, alimentatori a spirale rigida o flessibile, e nastri trasportatori per facilitare il movimento dei granuli. Non necessita di manutenzione ordinaria del filtro, ma comporta problemi di pulizia e usura dei meccanismi. È adatto solo per distanze limitate. - Trasporto a vuoto.
Utilizza la pressione differenziale per trasportare i granuli attraverso un sistema di condotte. Questo metodo si basa sulla creazione di un vuoto parziale generato da una pompa, che crea una differenza di pressione tra il punto di aspirazione e il punto di destinazione, consentendo il trasferimento del materiale.
Questa soluzione è la più efficace per supportare il lavoro delle aziende che trattano la plastica.
Vediamo ora quali tipologie di trasporto a vuoto esistono e come ottimizzarne l’efficienza.
Tipologie di trasporto a vuoto dei granuli plastici
Esistono diverse tipologie di trasporto per i granuli con la metodologia a vuoto indicati per l’industria plastica, ma tra le ultime innovazioni dotate di un sistema centralizzato spiccano:
- Alimentatore monofase.
Questo sistema comporta un investimento iniziale ridotto e consente la pulizia automatica del filtro, diminuendo tempi e costi di manutenzione. È dotato di un sistema di allarme automatico che segnala l’esaurimento del materiale. - Feeding kit.
Collegato al sistema di deumidificazione, permette di integrare deumidificazione e trasporto, gestendo fino a due stazioni con ricevitori. È ideale per installazioni vicino al sistema di deumidificazione, ma ha una portata limitata (100 kg/h) su brevi distanze. L’integrazione con un sistema VB può risolvere questi inconvenienti, pur limitando il collegamento a due stazioni. - Piccoli sistemi centralizzati trifase.
Questi sistemi di trasporto sono più complessi e includono un sistema per vuoto con filtro centralizzato a pulizia automatica e valvola di bypass, soffianti a canali laterali e un sistema di controllo 4.0 per diverse stazioni. La portata del materiale è illimitata e il sistema può gestire fino a 2, 4+4 o 9 stazioni. - Trasporto con sistema venturi.
Un alimentatore indipendente ad aria compressa adatto per il trasporto di materiali come masterbatch o additivi in granulo. È compatto e affidabile, può essere installato sopra una tramoggia di essiccazione e si adatta a produzioni ridotte. Permette il trasporto a flusso continuo con possibilità di regolare la potenza dell’aria e la velocità di trasporto. Assicura una separazione accurata delle polveri grazie al vortice ciclonico.
Ma come implementare i sistemi centralizzati a supporto del trasporto dei granuli di plastica?
I grandi impianti di trasporto centralizzato
Alcune aziende specializzate in trasporto dei granuli, come Vismec, operano per offrire macchine industriali per la lavorazione della plastica, progettando e realizzando dei grandi sistemi di trasporto centralizzato.
Questi macchinari vengono integrati con alcune soluzioni più innovative per consentire un trasporto più veloce e controllato.
Ad esempio, l’utilizzo e l’implementazione del sistema di controllo FW50 gestisce fino a 48 stazioni di trasporto per linea vuoto, con un eventuale sistema di riserva di emergenza, disponibile anche in versione touchscreen con controllo remoto e offre tre soluzioni di montaggio: con magnete, da tavolo e da parete.
L’inserimento del deumidificatore dry feed consente di erogare aria secca per evitare l’assorbimento di umidità durante il trasporto.
L’unità per vuoto o soffiante di emergenza previene invece il rischio di fermo macchina, mentre i ricevitori in acciaio inox sono disponibili in diverse dimensioni e dotati di sistemi di filtro e meccanismi di scarico, ispezione e pulizia ottimizzati.
Questi grandi sistemi di trasporto centralizzato offrono numerosi vantaggi per l’azienda.
Consentono di controllare e ottimizzare la logistica dei granuli plastici grazie ai sistemi di supervisione e gestione integrati; centralizzano la fase di filtrazione in un unico punto, mantengono pulito l’ambiente produttivo, riducono i consumi energetici, i tempi e i costi di manutenzione, generando un significativo risparmio per l’impresa.